Key outcomes
- Alchemite™ proposed an improved, more cost-efficient and environmentally-friendly alternative to today’s hardfacing material.
- Predictions were experimentally validated. The compositions selected differed considerably from existing materials.
- WAG has taken this material forward to industrial-scale performance trials.
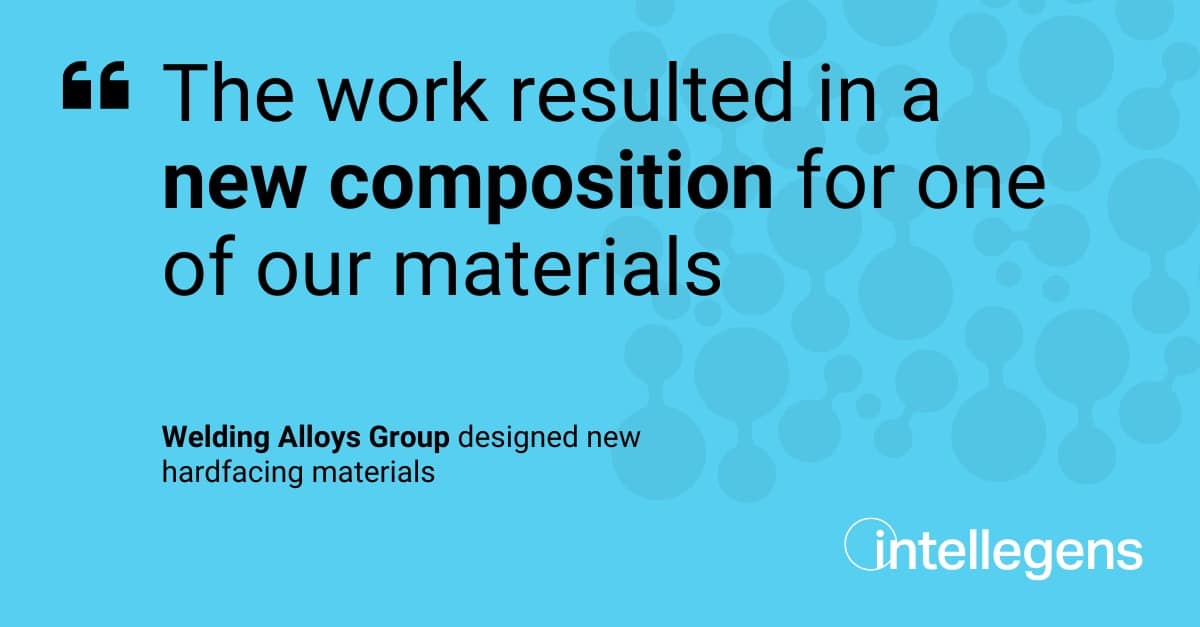
Summary
Wear is one of the most challenging problems faced by heavy industry. In mining alone, 17% of the consumed energy is used to combat wear failure, accounting for 2.7% of global CO2 emissions. One of the most common methods to combat wear is by welding highly alloyed consumables (hardfacing materials) onto the surfaces of components. These must meet stringent requirements on safety, cost, environmental impact, and performance. Wear performance is determined by a complex interaction of properties, therefore optimising cost/benefit for hardfacing materials is difficult.
Welding Alloys Group (WAG) and Intellegens applied machine learning to this problem, which resulted in the development of an improved hardfacing material with dramatic cost/benefit advantages, not only from a performance, but also from an environmental point of view.
Jean-Marie Bonnel and Mario Cordero, leaders of the project at Welding Alloys Group, agree that: “The combination of extensive technical know-how and experimental data provided by WAG, and the unique deep learning algorithms provided by Intellegens, resulted in a new composition that deviates considerably from any materials used in the past.”
Find out more
Mario Cordero from Welding Alloys Group presented on this case study at an Intellegens webinar on development of better, more sustainable materials.
Related information
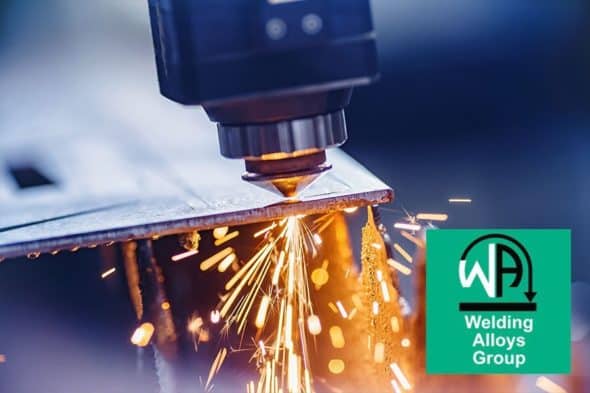