Intellegens is joining a new international collaborative project, RESTORE, which aims to develop sustainable-by-design remanufacturing processes and materials alongside supporting tools for the digitalisation of the remanufacturing ecosystem and value chain.
By extending product lifespans and enabling recycling of materials and process waste, the project will support the move towards a Circular Economy and the reduction of greenhouse gas emissions.
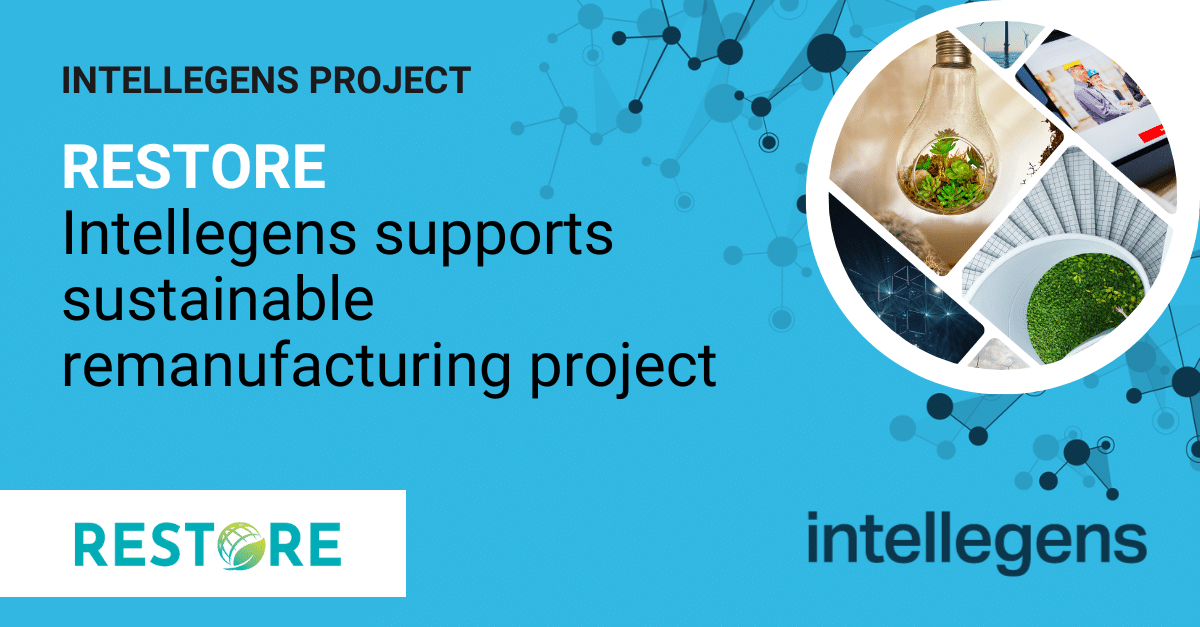
The technical focus of the project will be on advancing promising state-of-the-art cladding technologies, including laser direct energy deposition (DED), plasma transfer arc (PTA), and hybrids of these approaches. RESTORE will also produce wire feedstock with recycled content and enable the transfer of waste products such as machining swarf or unused powder into the melt pool. This paves the way for zero-waste remanufacturing technology at a reduced cost.
Intellegens will provide machine learning technology and expertise that helps to optimise material and process parameters when developing new manufacturing approaches. The Intellegens machine learning capabilities have previously been successfully applied to similar technical challenges in the design of hardfacing materials with project partner Welding Alloys Group.
“Intellegens are excited to collaborate with leading manufacturers in the RESTORE program,” says Intellegens CSO, Dr Gareth Conduit. “The project will enable further development of the machine learning algorithms underpinning Alchemite™ with a focus on sustainability and reduced carbon footprint.”
Further information
Project partners: EWF – The Coordinator, IRIS SRL, Fraunhofer SCAI, Dalforsan, Parida Consulting, Navtek, Welding Alloys, IREPA Laser, Gsmc (Inventage), Flowphys as, Aerobase Innovations Ab, Endurance Spa, Centro Ricerche Fiat Scpa, Phd Controlled Solutions Ab, Msc Scanning, Eit Manufacturing North Ab, Cranfield University, Lucchini Unipart Rail Limited, Technovative Solutions Limited, Intellegens.